(SPONSORED CONTENT)
When critical infrastructure fails, it is vital that repairs are carried out as quickly and safely as possible to minimise community disruption and maintain these essential services. However, during large scale events such as the COVID-19 pandemic or major earthquakes, getting supplies to an emergency construction site can prove difficult. Leading pipeline infrastructure company, Interflow, is helping local councils and water authorities provide optimum emergency services on-site through its robust, locally sourced solutions.
This time last year, the world was irrevocably changed by the COVID-19 pandemic. While many industries were temporarily shut down in a bid to curb the spread of the disease, water infrastructure asset owners such as local councils and water authorities maintained their essential services to keep their communities running.
With non-essential businesses compelled to close their doors and international transit coming to an abrupt halt, many Delivery Partners in the construction industry were faced with significant procurement and supply chain challenges.
Steadfast local solutions
Interflow’s General Manager – New Zealand, Blair Telfer, shares how Interflow’s reliable network throughout New Zealand and Australia enabled his team to respond to emergency situations throughout the pandemic.
“With our expertise and resources spread across Australia and New Zealand, we were able to continue sourcing materials throughout COVID-19,” he said.
“This was great for our customers, as it meant their critical pipeline infrastructure projects could continue as planned.”
A stand-out example of Interflow’s resilience and adaptability in action, the company carried out emergency works at Moa Point, Wellington, during the height of COVID-19.
Blair recalls how the company was able to remain on the front foot during the challenging times.
“As a self-performing contractor, who invests heavily in developing world-class pipeline infrastructure solutions in-house, our team was at the ready with a suite of solutions when COVID-19 arrived,” Blair said.
“Beyond our efficient supply chain, the solutions we offer have multiple benefits for our customers in times of crises.”
Trenchless technology tested in difficult conditions
During an emergency, it is important that the products, techniques, and technologies used will not only remedy the acute situation, but also provide a long-term solution once the dust settles.
During the critical repairs at Moa Point, Interflow used spiral wound liners, which were installed using trenchless technology. The same technologies were used by Interflow to repair New Zealand’s pipeline infrastructure following the devastating Canterbury earthquakes of 2010 and 2011.
“Spiral wound liners have stood the test of time and are now considered crucial for the lining of sewer and stormwater pipes, due to their quality-assured properties,” Blair said.
“Our spiral wound liner profile is manufactured in a factory under strict quality control processes. This means the structural integrity of the liner is consistent, whether it’s being tested in a factory or implemented in the field.”
Blair said other benefits of the spiral wound liner were the speed of installation, its ability to be applied in live flow conditions, the cost value when compared to open trenching methods, and the small site footprint.
“It is also less disruptive to the public, a fact that is particularly important when residents’ lives are turned upside-down by events such as the pandemic.”
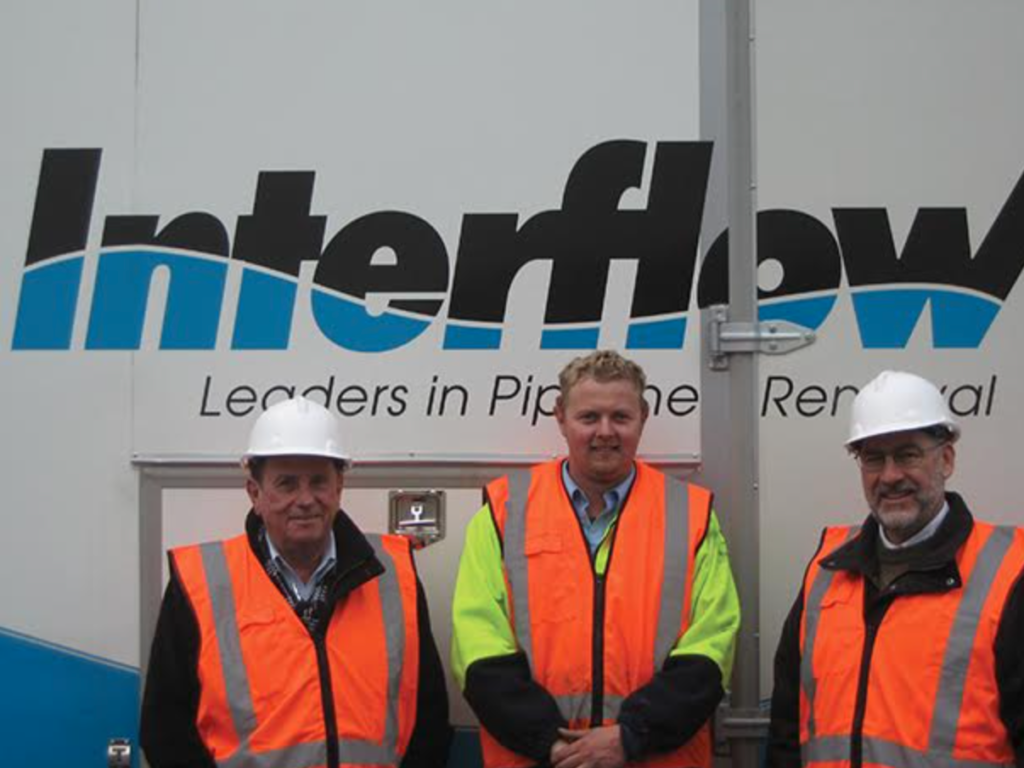
Dealing with the unexpected
These industry leading solutions, paired with Interflow’s self-performing capability, are enabling the company to support its customers’ communities and alleviate undue stress during difficult times.
“Our customers can rest assured that during emergency situations, our trusted team will be ready to mobilise and assist with all of their pipeline infrastructure needs,” Blair said.
Interflow’s emergency response during both the pandemic and the Canterbury earthquakes has provided the community with reliable, robust water infrastructure solutions that will stand the test of time.
“The success of the pipe lining carried out in Canterbury has given confidence to other councils and utilities that a spiral wound solution can withstand both earth movement as well as flooding and surcharging,” Blair said.
“The resilience of our products and solutions to aftershocks, some of high intensity, has also demonstrated to many of our customers that a spiral wound trenchless solution is often the most resilient to a natural disaster and is a viable long-term solution.”